Fasteners and Machining: Streamlining the Manufacturing Process
Fasteners and Machining: Streamlining the Manufacturing Process
Blog Article
Navigating the Globe of Fasteners and Machining: Techniques for Precision and Speed
In the intricate realm of fasteners and machining, the quest for precision and speed is a perpetual challenge that requires thorough focus to detail and calculated preparation. From comprehending the diverse range of fastener types to selecting optimum products that can stand up to extensive demands, each step in the process plays a pivotal duty in attaining the wanted end result.
Understanding Bolt Kind
When selecting bolts for a job, comprehending the numerous types available is essential for making sure ideal performance and dependability. Fasteners can be found in a vast variety of types, each designed for certain applications and demands. Bolts are used with nuts to hold materials together, while screws are functional bolts that can be used with or without a nut, depending upon the application. Nuts, on the various other hand, are internally threaded fasteners that friend with screws or screws, providing a safe and secure hold. Washers are necessary for distributing the lots of the fastener and preventing damages to the material being attached. Furthermore, rivets are permanent fasteners that are suitable for applications where disassembly is not needed. Recognizing the differences in between these fastener types is crucial for selecting the right one for the work, making sure that the connection is strong, sturdy, and reputable. By selecting the proper fastener kind, you can enhance the efficiency and durability of your task - Fasteners and Machining.
Selecting the Right Materials
Recognizing the importance of choosing the appropriate products is extremely important in making certain the optimal performance and dependability of the chosen bolt kinds talked about previously. When it pertains to fasteners and machining applications, the material choice plays a crucial role in identifying the general toughness, resilience, rust resistance, and compatibility with the designated atmosphere. Various materials use differing residential or commercial properties that can substantially influence the efficiency of the fasteners.
Typical materials utilized for fasteners include steel, stainless-steel, light weight aluminum, brass, and titanium, each having its unique toughness and weak points. Steel is renowned for its high toughness and toughness, making it appropriate for a large range of applications. Stainless steel provides outstanding corrosion resistance, perfect for settings susceptible to moisture and chemicals. Light weight aluminum is corrosion-resistant and light-weight, making it appropriate for applications where weight reduction is critical. Brass is often chosen for its aesthetic allure and superb conductivity. Titanium is recognized for its exceptional strength-to-weight ratio, making it perfect for high-performance applications. Selecting the appropriate product includes considering factors such as strength requirements, ecological problems, and budget restrictions to ensure the wanted efficiency and durability of the bolts.
Accuracy Machining Techniques
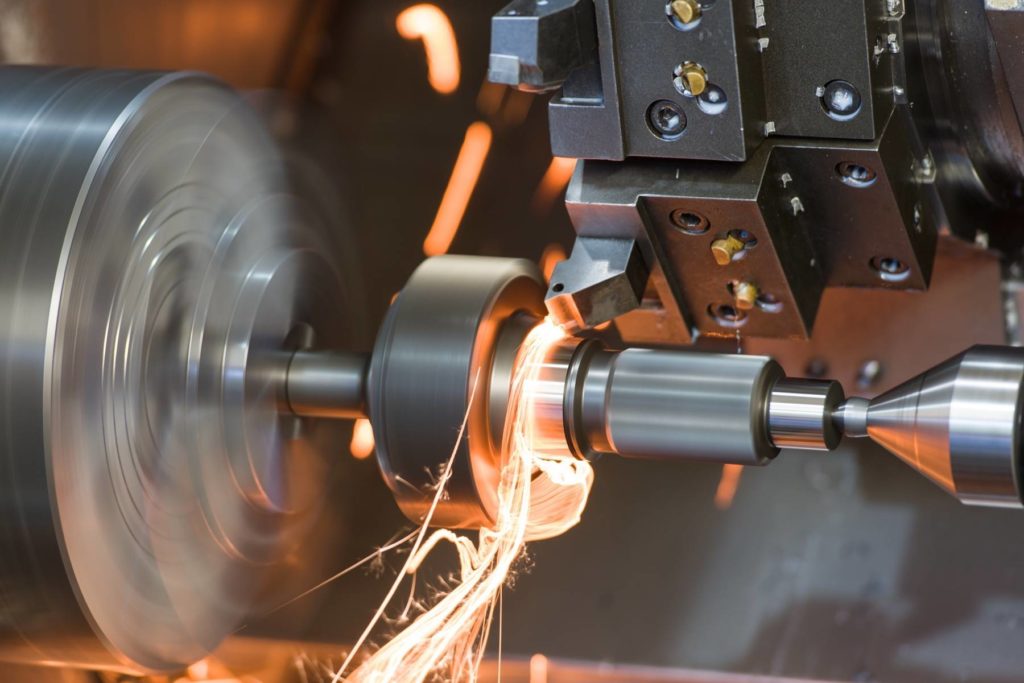
In enhancement to CNC machining, various other precision techniques like grinding, transforming, milling, and drilling play vital functions in fastener manufacturing. Grinding assists attain fine surface coatings and tight dimensional tolerances, while transforming is often utilized to develop cylindrical elements with specific diameters. Milling and boring procedures are essential for shaping and developing holes in bolts, guaranteeing they satisfy precise specifications and function properly.
Enhancing Speed and Effectiveness
To maximize fastener production processes, it is important to simplify procedures and apply efficient this methods that enhance accuracy machining strategies. One key method for enhancing rate and efficiency is the execution of lean production principles. By reducing waste and concentrating on constant renovation, lean practices help enhance and remove bottlenecks workflow. In addition, purchasing automation modern technologies can substantially enhance manufacturing speed. Automated systems can handle repeated jobs with precision and speed, allowing employees to concentrate on even more facility and value-added activities. Embracing Just-In-Time (JIT) supply monitoring can likewise enhance effectiveness by making sure that the ideal materials are offered at the best time, lessening excess stock and minimizing preparations. In addition, promoting a culture of collaboration and interaction amongst staff member can boost total efficiency by advertising transparency, analytic, and advancement. By integrating these methods, suppliers can attain a balance in between speed and accuracy, eventually improving their competitive edge in the bolt market.
Top Quality Control Steps
Applying extensive top quality control steps is critical in making sure the integrity and uniformity of fastener products in the manufacturing procedure. Quality assurance steps encompass numerous phases, beginning with the choice of resources to the last examination of the finished fasteners. One fundamental element of quality control is performing detailed material assessments to validate compliance with specifications. This involves assessing variables such as material durability, strength, and composition to guarantee that the fasteners meet industry criteria. In addition, monitoring the machining refines is important to copyright dimensional accuracy and surface area coating high quality. Using advanced technology, such as my site automatic assessment systems and accuracy measuring devices, can improve the accuracy and performance of high quality control procedures.
Normal calibration of devices and machinery is essential to preserve consistency in manufacturing and guarantee that fasteners satisfy the needed resistances. Executing stringent protocols for recognizing and attending to defects or non-conformities is vital in protecting against substandard items from going into the marketplace. By establishing a thorough quality assurance framework, makers can copyright the credibility of their brand and supply fasteners that fulfill the highest possible standards of performance and durability.
Conclusion
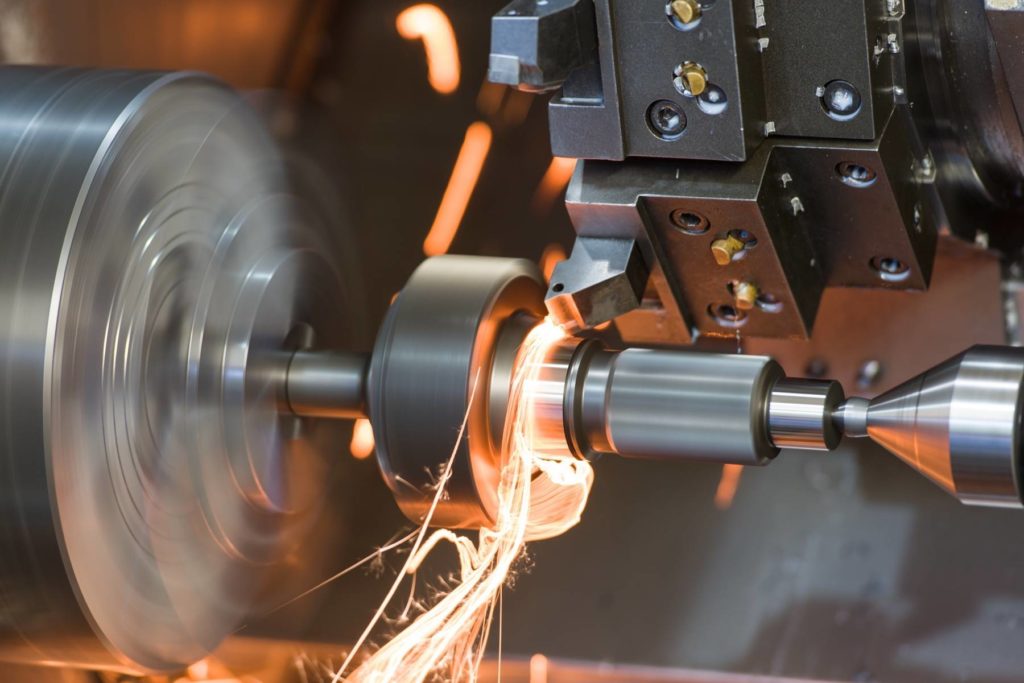
In the elaborate realm of fasteners and machining, the quest for precision and speed is a perpetual challenge that demands meticulous attention to detail and strategic planning. When it comes to bolts and machining applications, the product option plays an essential function in figuring out the general stamina, sturdiness, rust resistance, and compatibility with the intended environment. Precision machining involves different sophisticated approaches that make certain the limited resistances and specs required for bolts.In enhancement to CNC machining, other accuracy methods like grinding, turning, milling, and boring play crucial functions in bolt manufacturing.To optimize bolt production procedures, it is crucial to simplify procedures and execute efficient approaches that enhance accuracy machining techniques.
Report this page